In today’s fast-paced world, where workplaces serve as the backbone of every industry, the need for an organized and efficient environment has never been more critical. From bustling manufacturing plants to corporate offices and even the reception areas that greet clients, the presence of clutter and inefficiency can significantly drain productivity and create safety hazards. A disorganized workspace not only slows down workflows but can also lead to increased stress levels among employees, diminished morale, and potential accidents that could have been easily avoided. This is where the 5S methodology comes into play.
A transformative approach designed to revolutionize workspaces across various sectors. Originating in Japan as part of the Toyota Production System, 5S encompasses five core principles: Sort, Set in Order, Shine, Standardize, and Sustain. This step-by-step framework provides organizations with a systematic way to create cleaner, safer, and more productive environments. By implementing 5S, teams can streamline operations, reduce waste, and enhance collaboration, all while fostering a culture of continuous improvement.
In this article, we will explore each of the 5S principles in detail, illustrating how they can be practically applied to your workplace. We will also highlight real-world examples of organizations that have successfully embraced the 5S methodology, showcasing the significant improvements in efficiency and safety that can be achieved. Whether you’re looking to transform a single department or overhaul your entire organization, the principles of 5S can serve as a game-changer, leading to a more organized, efficient, and thriving workplace.
What is 5S?
The 5S methodology is a powerful framework for workplace organization and efficiency, rooted in five Japanese terms: Seiri (Sort), Seiton (Straighten), Seiso (Shine), Seiketsu (Standardize), and Shitsuke (Sustain). Each of these principles plays a crucial role in fostering a culture of organization, cleanliness, and continual improvement within the workplace. Originally developed as part of the Toyota Production System, 5S has evolved beyond its manufacturing origins to become a universally applicable tool for enhancing workplace efficiency across various industries.
- Seiri (Sort) involves identifying and separating essential items from non-essential ones. This principle encourages employees to declutter their workspaces by removing unnecessary tools, materials, and documents, thus streamlining processes and minimizing distractions.
- Seiton (Straighten) focuses on organizing and arranging items in a logical manner. By ensuring that every tool and resource has a designated place, employees can easily locate what they need when they need it, reducing wasted time and effort in searching for items.
- Seiso (Shine) emphasizes cleanliness and maintenance. This principle advocates for regular cleaning routines that not only keep the workplace tidy but also promote a sense of pride among employees. A clean environment enhances safety and helps in identifying potential issues, such as equipment malfunctions or hazards.
- Seiketsu (Standardize) involves establishing standardized procedures and best practices for maintaining the first three S’s. By creating clear guidelines and checklists, organizations can ensure that the improvements achieved through Sort, Straighten, and Shine are sustained over time.
- Shitsuke (Sustain) is about instilling discipline and a culture of continuous improvement among employees. This principle encourages everyone to take ownership of their workspace and adhere to the established standards, fostering a mindset of ongoing refinement and excellence.
The Benefits of Implementing 5S
One might wonder, why 5S? The answer lies in the immense benefits it offers:
- Improved Efficiency: When tools, files, and resources are neatly organized, time spent searching is drastically reduced. Efficiency naturally improves, and workflows become smoother.
- Enhanced Safety: By decluttering and arranging items logically, hazards like tripping or fire risks are minimized. A safer workspace is a more productive one.
- Higher Employee Morale: Employees thrive in environments that are clean, organized, and stress-free. A well-maintained workspace directly impacts job satisfaction and morale.
Step-by-Step Breakdown of 5S
Let’s dive deeper into each step of the 5S methodology to understand how it works and how it can be implemented.
Step 1: Sort (Seiri)
The first step in the 5S methodology is Sort, or Seiri, which focuses on eliminating unnecessary items from the workspace. This involves a comprehensive evaluation of all items present—tools, equipment, documents, and even furniture—to determine what is essential and what can be discarded or relocated.
Consider this step as akin to Marie Kondo’s decluttering philosophy for the workplace. The guiding question is: Does this item spark productivity? If the answer is no, it’s time to either discard it or store it elsewhere.
For example, imagine an office desk cluttered with outdated paperwork, unused gadgets, and broken stationery. Through sorting, employees can identify items that are no longer useful and remove them, thereby clearing the clutter and leaving only the essentials that contribute to a productive work environment. This not only enhances efficiency but also reduces stress, as a clean and organized workspace fosters better focus and concentration.
Step 2: Straighten (Seiton)
After decluttering, the next step is Straighten, or Seiton, which focuses on arranging the remaining items in a logical and orderly manner. Each item should have a designated place that aligns with its frequency of use; tools and resources that are utilized most often should be easily accessible.
To facilitate this organization, consider implementing visual aids such as labels, shadow boards, or digital tools that clearly indicate where each item belongs. This systematic approach reduces guesswork and ensures that team members can effortlessly retrieve what they need, ultimately saving time and increasing productivity.
For example, in a workshop setting, tools can be organized on shadow boards with outlines of each tool, making it immediately clear when an item is missing. This visual organization not only improves efficiency but also encourages a culture of responsibility among team members to return items to their designated locations after use.
Step 3: Shine (Seiso)
The Shine step, or Seiso, goes beyond mere aesthetics; it emphasizes the importance of maintaining a clean and safe working environment. Regular cleaning of workspaces, equipment, and tools is essential to prevent wear and tear and to uphold safety standards. A clean environment contributes to employee pride, morale, and productivity.
To instill a culture of cleanliness, consider turning cleaning into a daily habit. Even dedicating just five minutes each day to tidying up can lead to significant improvements in overall workplace cleanliness. For instance, teams can establish a quick cleanup routine at the end of each workday, ensuring that workstations are left organized and ready for the next day.
Incorporating cleaning as a routine task not only enhances safety by reducing the risk of accidents but also promotes a sense of ownership and pride in the workplace, leading to increased engagement among employees.
Step 4: Standardize (Seiketsu)
The Standardize step, or Seiketsu, is critical for ensuring that the improvements achieved in the previous three steps are maintained consistently over time. This involves developing clear protocols and schedules for tasks such as sorting, organizing, and cleaning.
Creating standard operating procedures, checklists, and schedules helps ensure that everyone is aligned and aware of their responsibilities. For instance, implementing a shared office calendar that highlights cleaning schedules or developing a checklist for restocking supplies can promote consistency across teams and departments.
Standardization also includes visual management techniques, such as color coding or signage, to remind employees of the 5S practices. By establishing these protocols, organizations can foster a culture of continuous improvement, where employees understand the importance of maintaining an organized and efficient workspace.
Step 5: Sustain (Shitsuke)
The final step, Sustain, or Shitsuke, transforms the 5S methodology from a one-time effort into an ongoing lifestyle. Sustaining 5S principles requires embedding them into the organizational culture through regular audits, employee training, and reinforcement from leadership.
Encouraging accountability is crucial in this step. This can be achieved by recognizing and rewarding employees who exemplify 5S principles, creating a sense of ownership and pride in maintaining a clean and organized workspace. Leadership should also model these behaviors, demonstrating their commitment to the 5S methodology.
Regular feedback sessions and reviews can help identify areas for improvement and maintain momentum. By cultivating a culture where 5S is a shared value, organizations can ensure that the benefits of this methodology are sustained over the long term, leading to enhanced productivity, safety, and employee satisfaction.
Why is 5S Essential for Modern Workplaces?
Workplaces today are vastly different from what they were a decade ago. The rise of hybrid work models, coworking spaces, and digital transformation has made organization even more critical. The 5S methodology adapts beautifully to these modern needs.
For instance, in a hybrid office setup, clear desk policies (Step 1: Sort) and hot-desking arrangements (Step 2: Straighten) can enhance productivity. Similarly, digital tools like Onfra’s desk booking system align with 5S by ensuring spaces are utilized effectively and clutter-free.
5S and Safety in the Workplace
Safety is a significant concern in any workspace. Disorganized spaces not only hinder productivity but also pose risks like trips, falls, or equipment damage. By implementing 5S, organizations can mitigate these risks.
Example: A manufacturing unit that adopts 5S eliminates scattered tools and materials, reducing the chances of accidents. Similarly, in an office setting, clean and decluttered pathways reduce tripping hazards.
Onfra’s Role in Optimizing Workplace Efficiency
Onfra, a Visitor Management Platform, plays a pivotal role in streamlining workplaces. Its innovative solutions, like the Onfra Pad App, exemplify the principles of 5S.
The Onfra Pad App transforms reception areas into self-service kiosks, reducing clutter and enhancing accessibility. This aligns perfectly with the 5S steps:
- Sort: Eliminates the need for bulky visitor logs and paperwork.
- Straighten: Streamlines visitor check-ins with a digital system.
- Shine: Maintains a clean and professional front desk area.
- Standardize: Provides consistent visitor management processes.
- Sustain: Encourages a culture of digital-first, organized operations.
Practical Tips for Implementing 5S
Getting started with 5S might seem daunting, but these tips can make the process smoother:
- Start Small: Focus on one area or department before scaling up.
- Involve Employees: Encourage team participation to foster ownership.
- Leverage Visual Aids: Use charts, labels, and diagrams to reinforce 5S steps.
- Set Clear Goals: Define what success looks like for your 5S initiative.
- Monitor Progress: Regularly assess and adjust your approach.
5S in Action: Real-Life Examples
The beauty of 5S is its versatility. Businesses across industries have successfully adopted it:
- Manufacturing: A factory reduced equipment downtime by 20% by implementing Step 2: Straighten.
- Corporate Offices: An IT firm saved 15 hours per week by decluttering shared storage areas.
- Healthcare: A hospital improved patient care by standardizing medical supply storage.
Overcoming Challenges in 5S Implementation
Every change comes with challenges, and 5S is no exception. Common barriers include resistance to change, inconsistent application, and lack of leadership support.
Solutions:
- Offer training sessions to educate employees about 5S benefits.
- Assign 5S champions to monitor progress.
- Regularly communicate successes to build momentum.
Measuring the Impact of 5S
To ensure your 5S efforts are effective, track key performance indicators (KPIs) such as:
- Reduction in safety incidents.
- Improved turnaround times.
- Employee satisfaction scores.
- Feedback on workplace organization.
Integrating Technology with 5S
Technology can significantly enhance 5S implementation. Tools like Onfra’s desk booking system and visitor management platform automate processes, reduce physical clutter, and ensure seamless operations.
For example, digital tools can help with Step 4: Standardize by automating cleaning schedules or tracking equipment maintenance.
How 5S Enhances Productivity and Collaboration
An organized workspace isn’t just about individual productivity—it’s about fostering collaboration. When everyone knows where to find tools or resources, teamwork becomes more fluid.
For example, a marketing team that follows 5S principles can quickly access shared files, reducing downtime and improving project delivery.
Maintaining 5S Culture Long-Term
Consistency is the key to 5S success. Organizations should:
- Conduct regular audits to ensure compliance.
- Celebrate employees who champion 5S practices.
- Incorporate 5S training into onboarding processes.
Conclusion
The 5S methodology is more than just a framework—it’s a cultural shift that drives efficiency, safety, and productivity. By focusing on organization and continuous improvement, businesses can create workplaces that empower employees and deliver results. Whether you’re managing a manufacturing unit or a modern office, 5S can transform your space and operations. Start your 5S journey today and unlock its potential for your organization.
FAQs
1. What is the 5S methodology in simple terms?
The 5S methodology is a system for organizing workplaces to improve efficiency and safety. It involves five steps: Sort, Straighten, Shine, Standardize, and Sustain.
2. How does 5S improve workplace safety?
By removing clutter and arranging items logically, 5S minimizes hazards such as trips, falls, or equipment damage. Regular cleaning also ensures safer environments.
3. Can 5S be applied in digital workspaces?
Absolutely. 5S principles can be applied to organize files, emails, and workflows in digital environments, enhancing productivity and reducing digital clutter.
4. How does Onfra support 5S principles?
Onfra provides digital tools like desk booking systems and visitor management platforms that streamline operations, reduce clutter, and maintain organized workflows.
5. What industries can benefit from 5S?
5S is versatile and can be applied in industries such as manufacturing, healthcare, retail, corporate offices, and even education.
6. How long does it take to implement 5S?
The time frame varies depending on the size and complexity of the workplace. It’s best to start small and gradually scale up for sustainable results.
7. What are common challenges in 5S implementation?
Resistance to change, inconsistent application, and lack of leadership support are common challenges. Training and regular communication can help overcome these barriers.
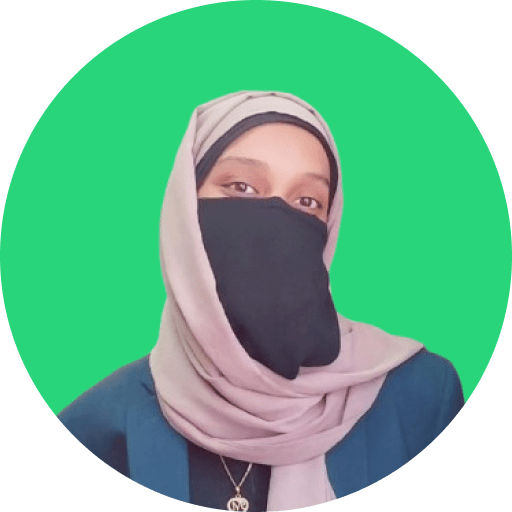
A subject matter expert in facilities, workplace, culture, tech, and SaaS, I create impactful content strategies that enhance startup retention and foster strong connections. With a blend of technical expertise and creativity, I drive engagement and loyalty. Always eager for challenges and make a lasting impact.