Predictive maintenance is rapidly changing how industries manage and maintain their equipment. From manufacturing floors to transportation fleets, artificial intelligence (AI) has become a valuable asset for anticipating equipment failures and reducing maintenance costs. By leveraging AI, predictive maintenance solutions use real-time data to forecast issues before they arise, ultimately enhancing productivity, safety, and profitability. This guide explores AI’s role in predictive maintenance, its benefits, real-world applications, and future trends.
What is Predictive Maintenance?
Definition and Importance
Predictive maintenance is a proactive approach that uses data analysis and real-time monitoring to predict when equipment failures might occur. This allows maintenance teams to make repairs before any actual breakdowns happen, reducing downtime and saving costs. In contrast to reactive maintenance (fixing issues after they occur) or preventive maintenance (scheduled servicing regardless of need), predictive maintenance offers a more precise, data-driven approach.
Traditional Maintenance Approaches vs. Predictive Maintenance
Traditional maintenance typically involves scheduled checks or reactive repairs once equipment malfunctions. While preventive maintenance helps avoid breakdowns, it often results in unnecessary maintenance, wasting time and resources. Predictive maintenance, on the other hand, focuses on condition-based data, using AI to predict optimal maintenance times and eliminate unnecessary servicing, improving efficiency and lowering costs.
The Role of Artificial Intelligence in Predictive Maintenance
AI and Machine Learning in Maintenance Prediction
AI and machine learning (ML) algorithms analyze historical and real-time data from equipment sensors to detect patterns and forecast potential failures. Over time, machine learning models become more accurate, learning to identify subtle changes that might signal an impending malfunction. This predictive ability empowers organizations to perform maintenance precisely when it’s needed, reducing downtime and enhancing productivity.
How AI Enhances Maintenance Accuracy
AI improves predictive maintenance accuracy by analyzing complex datasets collected from sensors and monitoring equipment. Traditional monitoring systems might miss subtle variations, but AI’s ability to detect these changes enables a more proactive approach. This data-driven precision allows teams to plan repairs at optimal times, ultimately increasing equipment reliability.
Key Components of AI-Driven Predictive Maintenance
Data Collection and Sensor Integration
Data collection is foundational to AI-based predictive maintenance. Sensors installed on equipment capture various performance metrics, including temperature, vibration, and pressure. This data is transmitted to AI systems for analysis, providing insights into equipment health. Advanced systems can integrate data from multiple sensors, offering a comprehensive view of the equipment’s condition.
Machine Learning Algorithms for Predictive Analysis
Machine learning algorithms are at the heart of predictive maintenance. By analyzing historical and real-time data, these algorithms identify trends and anomalies, predicting when issues may arise. For example, ML models trained on historical breakdown data can recognize warning signs and alert maintenance teams, enabling preemptive action.
Real-Time Monitoring and Analytics
AI-driven predictive maintenance leverages real-time monitoring, allowing instant alerts if equipment shows signs of stress or impending failure. This proactive monitoring is essential in critical industries like manufacturing, where equipment uptime directly impacts production schedules and revenue. Real-time analytics further enhance predictive capabilities by enabling immediate responses to emerging issues.
How Predictive Maintenance Works with AI
AI-powered predictive maintenance follows a structured process:
- Data Collection: Sensors installed on equipment continuously collect operational data.
- Data Processing: This data is processed and fed into machine learning models.
- Analysis: AI algorithms analyze the data, looking for patterns or irregularities that may indicate potential issues.
- Prediction and Alert: The AI system notifies the maintenance team when a potential problem is detected.
- Action: Maintenance teams can intervene, addressing the issue before it impacts operations.
AI’s Role in Diagnosing Potential Issues
Beyond predicting maintenance needs, AI can also help diagnose specific issues by analyzing data patterns. For instance, if a particular piece of equipment shows unusual vibration levels, AI may determine that it’s due to misalignment or worn-out components. This targeted approach makes repairs more effective and efficient.
Benefits of AI in Predictive Maintenance
Reduced Downtime and Costs
Unplanned downtime is costly for industries reliant on continuous operation. AI-powered predictive maintenance allows organizations to prevent unexpected breakdowns by scheduling repairs at optimal times. By identifying potential issues early, companies can minimize downtime, ensuring that equipment remains operational and efficient.
Increased Asset Lifespan
AI-driven predictive maintenance ensures that assets are only serviced when necessary, avoiding over-maintenance. This approach prevents wear and tear from excessive handling and extends the lifespan of machinery. With a more extended asset life, companies can reduce capital expenditures on replacements.
Enhanced Safety and Reliability
Predictive maintenance also improves workplace safety. When machinery malfunctions, it can lead to dangerous situations for operators and maintenance staff. By addressing equipment issues before they become critical, AI-based predictive maintenance reduces the risk of accidents and enhances operational reliability.
AI Technologies Used in Predictive Maintenance
Machine Learning Algorithms
Machine learning is fundamental to predictive maintenance, enabling systems to analyze large volumes of data and detect failure patterns. Through supervised and unsupervised learning, these algorithms continuously improve, resulting in more accurate and reliable predictions over time.
Natural Language Processing (NLP)
Natural Language Processing (NLP) is used to analyze historical maintenance logs and manuals, extracting valuable information that can improve AI predictions. For instance, NLP can identify recurring issues in maintenance logs, offering additional context for predicting equipment failures.
Computer Vision
Computer vision is used to monitor equipment visually. For example, cameras can detect wear, leaks, or cracks in machinery. AI analyzes these images, identifying potential issues without the need for manual inspection, making it especially useful in large-scale operations where physical monitoring would be impractical.
Industries Benefiting from AI-Driven Predictive Maintenance
Manufacturing
In the manufacturing industry, predictive maintenance is crucial. Equipment failures can halt production, resulting in missed deadlines and financial losses. AI-powered proactive maintenance approach allows manufacturers to avoid downtime by identifying issues early, keeping production on track.
Oil and Gas
The oil and gas industry relies on complex, high-value equipment that operates in harsh environments. AI-driven predictive maintenance minimizes the risk of failure in this sector, helping companies maintain equipment efficiently and avoid costly breakdowns.
Transportation and Logistics
For transportation and logistics companies, vehicle reliability is paramount. AI-powered predictive maintenance helps these companies ensure that their fleets are in peak condition, reducing the likelihood of breakdowns and enhancing service reliability.
Challenges in Implementing AI in Predictive Maintenance
Data Quality and Collection Issues
One of the main challenges in implementing AI-driven proactive maintenance approach is data quality. For accurate predictions, the data used by AI systems must be complete and accurate. Inconsistent or incomplete data can compromise prediction quality, making it challenging to achieve reliable outcomes.
High Implementation Costs
The cost of implementing proactive maintenance approach can be a barrier, especially for small and medium-sized businesses. Sensors, AI software, and data storage can add to the initial investment, but many companies find the cost savings from reduced downtime and extended equipment life make it worthwhile over time.
Overcoming Predictive Maintenance Challenges with AI
Improving Data Quality
Organizations can improve data quality by investing in high-quality sensors and establishing data collection protocols. Ensuring consistent data is critical, as it enables AI algorithms to make accurate predictions and minimizes the risk of faulty alerts.
Minimizing Costs
For businesses concerned with high costs, AI-driven proactive maintenance approach can be introduced in phases. By initially focusing on critical equipment, companies can reduce risk and cost before scaling the system to other assets. Over time, the savings generated by reduced maintenance expenses often offset implementation costs.
The Future of Predictive Maintenance with AI
The Potential of IoT and AI Integration
The Internet of Things (IoT) is set to play an essential role in the future of proactive maintenance approach. IoT devices provide a continuous flow of data from remote locations, which AI systems can analyze to deliver real-time insights. By integrating IoT with AI, industries can enhance predictive capabilities, monitor equipment from afar, and streamline operations.
Advancements in AI Algorithms
As AI algorithms become more sophisticated, their predictive accuracy will continue to improve. New models and advanced machine learning techniques will further enhance AI-driven proactive maintenance approach, making it an even more valuable asset for organizations.
Case Studies: Success Stories of AI in Predictive Maintenance
Manufacturing Industry Example
In the manufacturing sector, one company implemented AI-powered proactive maintenance approach, resulting in a 30% reduction in equipment downtime. By predicting when machinery was likely to fail, the company avoided costly repairs and kept production on schedule, ultimately boosting revenue.
Transportation Sector Example
A logistics company adopted AI-driven proactive maintenance approach for its fleet, significantly reducing vehicle breakdowns. With AI’s predictive insights, the company could perform timely repairs, improving delivery reliability and customer satisfaction.
How AI Predictive Maintenance Aligns with Sustainability Goals
Reduced Energy Consumption
Predictive maintenance helps optimize energy usage by ensuring equipment operates at peak efficiency. This reduces the energy required for operations, lowering overall energy consumption and supporting sustainability initiatives.
Lower Carbon Emissions
Efficient equipment produces fewer carbon emissions, as well-maintained machinery operates more cleanly and efficiently. By extending equipment life and preventing unnecessary replacements, predictive maintenance also reduces the environmental impact of manufacturing new parts and machinery.
Key Considerations When Choosing an AI-Powered Predictive Maintenance Solution
Scalability
When implementing an AI-powered proactive maintenance approach, scalability is a vital factor to consider. As businesses grow and operations expand, maintenance needs inevitably increase—often alongside the complexity and volume of equipment and machinery that require upkeep. A scalable predictive maintenance solution allows companies to start small and gradually build up as needs evolve, accommodating additional assets, equipment, and sensors without performance issues or extensive reconfiguration.
A scalable solution should support the integration of new data sources and types, such as IoT sensors and equipment monitoring tools, which help capture more comprehensive data as the system grows. This flexibility not only saves time and resources by avoiding frequent system overhauls but also ensures that maintenance processes remain consistent and reliable as the scope of operations broadens. For companies looking to grow their asset base or expand their facilities, a scalable AI solution offers peace of mind, knowing the system can adapt to meet increasing demand.
Moreover, scalability enhances the cost-efficiency of predictive maintenance systems. Companies can invest in a solution with minimal upfront resources and expand as necessary, paying only for what they need as they go. This cost-effective approach makes it possible to maintain equipment health and maximize uptime while aligning with business growth goals. Ultimately, selecting an AI-powered predictive maintenance solution with robust scalability capabilities enables businesses to future-proof their maintenance strategies, ensuring continuous and efficient equipment management well into the future.
Integration Capabilities
Seamless integration with existing tools is another critical aspect of choosing an AI-powered proactive maintenance approach. Many companies rely on established systems for asset management, workflow coordination, and operational reporting. An ideal proactive maintenance approach solution should integrate effortlessly with these tools, whether it’s an enterprise resource planning (ERP) platform, a computerized maintenance management system (CMMS), or IoT networks.
Smooth integration minimizes the risk of operational disruptions, allowing companies to transition to AI-powered proactive maintenance approach without overhauling their entire infrastructure or retraining staff on multiple new systems. For instance, a maintenance team can continue using familiar software while gaining the added benefits of proactive maintenance approach insights, such as real-time equipment health alerts or predictive failure warnings. This approach not only simplifies adoption but also enhances operational efficiency by consolidating maintenance insights within existing workflows.
Additionally, effective integration allows for more comprehensive data analysis. When AI-powered predictive maintenance solutions are seamlessly integrated with existing systems, data from different sources can be combined, offering a more holistic view of equipment performance and maintenance needs. This centralized data visibility enables better decision-making and facilitates proactive maintenance actions across departments.
Ultimately, a predictive maintenance solution with strong integration capabilities allows companies to maximize the benefits of AI without the hassle of disruptive changes. This adaptability supports efficient implementation, enhances cross-functional collaboration, and leverages existing infrastructure for streamlined, AI-driven maintenance management.
Conclusion
The role of AI in predictive maintenance is transforming how industries approach equipment management. By leveraging data-driven insights, AI-based predictive maintenance helps organizations avoid costly downtime, extend asset life, and enhance operational safety. As AI and IoT technologies continue to advance, predictive maintenance will become an indispensable tool, supporting efficiency and sustainability across multiple industries.
FAQs
1. How does proactive maintenance approach save costs?
proactive maintenance approach reduces costs by preventing unexpected equipment breakdowns and minimizing repair expenses, enabling efficient resource allocation.
2. Can proactive maintenance approach operate without AI?
While proactive maintenance approach can function without AI, AI significantly improves accuracy by analyzing vast datasets that are challenging to process manually.
3. Which industries benefit most from AI-driven predictive maintenance?
Industries such as manufacturing, oil and gas, and transportation benefit the most due to their reliance on high-value, continuously operating equipment.
4. Is predictive maintenance scalable?
Yes, AI-driven proactive maintenance approach solutions are highly scalable, adaptable to various industries and operational sizes.
5. How does predictive maintenance support sustainability goals?
proactive maintenance approach minimizes energy consumption and emissions by keeping equipment operating efficiently, supporting environmental and sustainability goals.
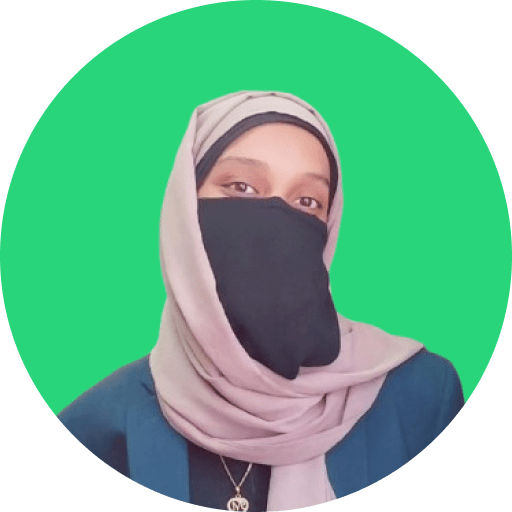
A subject matter expert in facilities, workplace, culture, tech, and SaaS, I create impactful content strategies that enhance startup retention and foster strong connections. With a blend of technical expertise and creativity, I drive engagement and loyalty. Always eager for challenges and make a lasting impact.