In today’s fast-paced industrial landscape, where competition is fierce and profit margins are tight, manufacturers are constantly seeking ways to streamline their operations and maximize productivity. One powerful tool that has gained widespread adoption is Total Productive Maintenance (TPM), a comprehensive performance improvement strategy that engages all employees in the maintenance process.
TPM is a proactive approach that aims to eliminate unplanned downtime, reduce maintenance costs, and improve overall equipment effectiveness. By shifting the responsibility of routine and preventative maintenance from the maintenance team to the operators who work with the equipment daily, TPM empowers employees to take ownership of their machines and ensure they operate at peak performance.
This article will delve into the principles of TPM, explore its benefits, and provide a step-by-step guide for implementing this powerful methodology in your organization.
The Foundations of TPM: The 5S Methodology
Total Productive Maintenance is built upon the solid foundation of the 5S methodology, a lean management technique that focuses on workplace organization and efficiency. The 5S principles, which originated in Japan, are as follows:
- Sort (Seiri): Eliminate unnecessary items from the workplace, keeping only what is essential for daily operations.
- Set in Order (Seiton): Arrange necessary items in a neat and orderly manner, making them easily accessible when needed.
- Shine (Seiso): Regularly clean and inspect the work area, maintaining a safe and sanitized environment.
- Standardize (Seiketsu): Establish standard procedures for conducting the first three S’s, ensuring consistency across the organization.
- Sustain (Shitsuke): Continuously apply the 5S principles, making them a habit and part of the organizational culture.
By implementing the 5S methodology, organizations create a solid foundation for TPM, ensuring that the workplace is organized, clean, and efficient, setting the stage for the implementation of the eight pillars of TPM.
The Eight Pillars of TPM
Resting upon the 5S foundation, TPM is supported by eight pillars that guide organizations in their quest for equipment optimization and overall performance improvement. These pillars are:
1. Autonomous Maintenance
Autonomous maintenance empowers operators to take responsibility for the basic care and maintenance of their equipment. This includes tasks such as cleaning, lubricating, and inspecting machines on a regular basis. By involving operators in these activities, they gain a deeper understanding of their equipment, enabling them to identify potential issues early and take corrective action before they escalate into major problems.
2. Planned Maintenance
Planned maintenance involves creating a schedule for routine maintenance tasks based on the predicted or measured failure rates of equipment. This proactive approach helps to minimize unplanned downtime by addressing potential issues before they occur. By considering factors such as machine age and usage, maintenance teams can optimize their schedules and ensure that equipment is well-maintained throughout its lifecycle.
3. Quality Maintenance
Quality maintenance focuses on preventing equipment-related errors and defects during the production process. By monitoring machine performance and implementing automated systems to detect anomalies, organizations can identify and address issues before they impact product quality. When errors do occur, a root cause analysis is conducted to identify and eliminate the underlying causes, preventing their recurrence.
4. Focused Improvement
Focused improvement involves the formation of small, cross-functional teams that analyze production activities and identify opportunities for improvement. These teams work together to eliminate waste, streamline processes, and enhance overall equipment effectiveness. By engaging employees at all levels, focused improvement taps into the collective knowledge and expertise of the organization, driving continuous improvement.
5. Early Equipment Management
Early equipment management emphasizes the importance of incorporating lessons learned from previous production and maintenance activities into the design and procurement of new equipment. By collaborating with suppliers, manufacturers, and other stakeholders, organizations can ensure that new machinery meets or exceeds performance expectations, minimizing the risk of costly modifications or replacements down the line.
6. Training and Education
Effective implementation of TPM requires a well-trained and knowledgeable workforce. The training and education pillar focuses on providing employees at all levels with the necessary skills and knowledge to effectively implement and maintain TPM practices. This includes training on the 5S methodology, autonomous maintenance, and other TPM-related techniques, ensuring that everyone understands their role in the success of the program.
7. Safety, Health, and Environment
A safe and healthy work environment is essential for the success of any TPM initiative. This pillar focuses on creating and maintaining a workplace that is free from hazards, minimizing the risk of accidents and injuries. By addressing safety concerns and promoting a culture of health and well-being, organizations can improve employee morale, reduce absenteeism, and ensure that production runs smoothly without interruptions.
8. TPM in Administration
While TPM is often associated with manufacturing and production environments, its principles can be applied to administrative functions as well. The TPM in administration pillar explores ways in which office workers, managers, and support staff can implement TPM practices to increase productivity, reduce waste, and enhance overall organizational performance. This may include streamlining administrative processes, optimizing resource utilization, and fostering a culture of continuous improvement across all departments.
The Benefits of TPM
Implementing Total Productive Maintenance can yield a wide range of benefits for organizations, including:
- Reduced maintenance costs: By shifting to a proactive maintenance approach, organizations can minimize the need for costly emergency repairs and unplanned downtime.
- Improved equipment reliability: Regular maintenance and operator involvement in equipment care can extend the lifespan of machines and reduce the frequency of breakdowns.
- Enhanced product quality: With fewer equipment-related defects and errors, organizations can produce higher-quality products, reducing waste and improving customer satisfaction.
- Increased productivity: Longer equipment uptime and smoother production processes lead to higher output and better utilization of resources.
- Safer work environment: By addressing safety concerns and promoting a culture of health and well-being, TPM helps to create a workplace that is free from hazards and promotes employee well-being.
- Improved employee morale: By engaging employees in the maintenance process and empowering them to take ownership of their equipment, TPM can boost morale and foster a sense of pride and accomplishment among the workforce.
- Reduced environmental impact: Well-maintained equipment operates more efficiently, consuming fewer resources and generating less waste, thereby reducing the organization’s environmental footprint.
Implementing TPM: A Step-by-Step Guide
Here is a step-by-step guide to help you get started:
1. Secure management commitment
Successful TPM implementation requires the full support and commitment of management. Engage with senior leaders to ensure they understand the benefits of TPM and are willing to allocate the necessary resources and support to make the initiative a success.
2. Establish a TPM steering committee
Form a cross-functional steering committee that will be responsible for overseeing the TPM implementation process. This committee should include representatives from various departments, including production, maintenance, quality, and safety, to ensure a holistic approach to implementation.
3. Conduct a baseline assessment
Before embarking on the TPM journey, it is essential to understand the current state of your organization’s maintenance practices and equipment performance. Conduct a thorough assessment to identify strengths, weaknesses, and areas for improvement. This baseline assessment will serve as a benchmark for measuring the success of your TPM initiative.
4. Develop a TPM implementation plan
Based on the findings of your baseline assessment, develop a comprehensive TPM implementation plan that outlines the specific steps, timelines, and resources required to achieve your goals. This plan should include clear objectives, milestones, and performance metrics to track progress and ensure accountability.
5. Implement the 5S methodology
Begin by implementing the 5S methodology in the pilot area(s) you have identified. Engage employees in the process of sorting, setting in order, shining, standardizing, and sustaining their work areas. Provide training and support to ensure that the 5S principles are properly understood and consistently applied.
6. Introduce autonomous maintenance
Once the 5S foundation is in place, begin implementing autonomous maintenance practices. Train operators on basic equipment care and maintenance tasks, such as cleaning, lubricating, and inspecting their machines. Provide the necessary tools and resources to support these activities, and establish clear roles and responsibilities.
7. Implement planned maintenance
Develop and implement a planned maintenance program based on the predicted or measured failure rates of your equipment. Collaborate with maintenance teams to create a schedule that optimizes resource utilization and minimizes disruptions to production.
8. Measure and monitor performance
Establish clear performance metrics and regularly monitor progress to ensure that your TPM initiative is delivering the desired results. Use tools such as overall equipment effectiveness (OEE) to track improvements in equipment reliability, quality, and productivity.
9. Continuously improve
TPM is an ongoing process, not a one-time event. Continuously seek ways to improve your practices, learn from successes and failures, and adapt to changing conditions. Engage employees at all levels in the continuous improvement process, tapping into their knowledge and expertise to drive innovation and enhance performance.
Conclusion
Total Productive Maintenance is a powerful tool for organizations looking to optimize equipment performance, reduce maintenance costs, and improve overall productivity. By engaging employees in the maintenance process and fostering a culture of continuous improvement, TPM helps organizations to achieve their goals and stay competitive in today’s fast-paced business environment.
Implementing TPM requires commitment, patience, and a willingness to adapt, but the benefits are well worth the effort. By following the principles of the 5S methodology and the eight pillars of TPM, organizations can create a well-organized, efficient, and safe work environment that supports their long-term success.
As you embark on your TPM journey, remember to start small, secure management commitment, and engage employees at all levels. With a solid implementation plan and a focus on continuous improvement, your organization can reap the benefits of Total Productive Maintenance and take its performance to new heights.
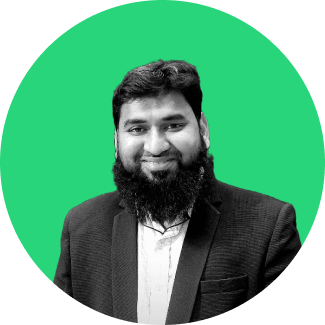
CEO of onfra.io, brings a wealth of expertise in technology and entrepreneurship. With a passion for innovation, Aadil leads the team at onfra.io in revolutionizing visitor management solutions.