Efficient operations depend heavily on the smooth functioning of equipment, infrastructure, and workspaces. Regular, planned maintenance tasks are crucial for preventing unexpected breakdowns, avoiding costly repairs, and minimizing disruptions. However, despite their importance, many organizations struggle to stay on top of maintenance schedules, resulting in inefficiencies and rising operational costs.
If your business struggles with missed maintenance tasks, you’re not alone. It’s a common issue, but the consequences can be severe. By examining why tasks are missed and how you can improve your maintenance strategy, you can keep your operations running smoothly. In this comprehensive guide, we will not only explore the reasons behind missed maintenance tasks but also introduce you to how platforms like Onfra, a Visitor Management System (VMS) that includes desk booking and kiosk functionality, can help you streamline your processes and eliminate these oversights.
Understanding the Importance of Planned Maintenance
What is Planned Maintenance?
Planned maintenance is a proactive approach to maintaining equipment and infrastructure. It involves scheduling regular inspections, servicing, repairs, and replacements based on a predetermined timeline. The purpose is to address potential issues before they escalate into serious problems that could disrupt operations.
By carrying out maintenance tasks at scheduled intervals, businesses can extend the lifespan of their assets, improve operational efficiency, and ensure safety compliance. This approach is different from reactive maintenance, which addresses problems only after they occur, often leading to downtime and emergency repairs.
Why Do Businesses Rely on Planned Maintenance?
Businesses rely on planned maintenance for several reasons. First, it minimizes equipment downtime, ensuring that machines, systems, and workspaces are available when needed. Second, it prevents unexpected breakdowns, which can lead to costly emergency repairs and replacement expenses. Lastly, planned maintenance helps businesses comply with safety regulations, reducing the risk of accidents and ensuring the well-being of employees.
In highly regulated industries, like manufacturing, healthcare, and transportation, planned maintenance is not just a best practice but often a legal requirement. Failure to maintain equipment properly can result in regulatory fines, loss of business licenses, and reputational damage.
The Cost of Missed Maintenance Tasks
When a business neglects its maintenance schedule, the cost can quickly add up. Missed maintenance tasks result in:
- Increased Repair Costs: Small issues that could have been fixed during routine maintenance may grow into bigger, more expensive problems.
- Operational Downtime: Equipment failure can halt production lines or disrupt service delivery, leading to lost revenue.
- Reduced Equipment Lifespan: Neglecting maintenance accelerates wear and tear, shortening the lifespan of expensive machinery and systems.
- Safety Hazards: Missed maintenance can create unsafe working conditions, increasing the risk of accidents and potential legal liability.
Businesses may find themselves constantly firefighting—dealing with urgent breakdowns and costly repairs—rather than following a structured, cost-effective maintenance plan.
Common Reasons Why Maintenance Tasks Are Missed
Lack of Proper Scheduling
One of the most common reasons for missed maintenance tasks is poor scheduling. Many organizations still rely on manual or outdated scheduling systems that fail to provide a clear overview of upcoming tasks. This can result in conflicting schedules, forgotten tasks, and inefficiencies in assigning maintenance work.
For instance, if a team doesn’t have access to a centralized scheduling system, it’s easy to overlook key tasks. Without a reliable schedule, businesses may also fail to prioritize critical equipment, leading to breakdowns that could have been easily avoided.
Poor Communication Between Teams
Effective communication is essential in any business operation, especially when it comes to maintenance management. Maintenance tasks often involve multiple departments—facilities, IT, operations, and even external contractors. Without clear communication between these parties, it’s easy for tasks to be delayed or forgotten.
For example, if the operations team isn’t notified about upcoming maintenance, they may continue using equipment that needs servicing, leading to unintentional damage. Similarly, if facilities management doesn’t communicate maintenance schedules to other departments, workspaces may be unavailable during critical periods.
Human Error in Monitoring Systems
Relying on human input alone to track and monitor maintenance schedules is risky. People make mistakes, and when maintenance tasks are recorded manually, there is a higher chance of oversight. A missed deadline, incorrect data entry, or failure to communicate changes can result in missed maintenance, and the consequences can be significant.
This is where automation comes into play. By using automated systems, businesses can reduce the risk of human error and ensure that maintenance tasks are not overlooked.
Signs That Your Maintenance Strategy Needs Improvement
How can you tell if your current maintenance strategy is failing? Here are some signs to watch out for:
Increase in Equipment Downtime
If your equipment is experiencing frequent downtime, this is a red flag that your maintenance schedule isn’t being followed. Downtime can be costly, as it halts operations and reduces productivity. Frequent downtime is often a sign that routine maintenance is being missed, allowing minor issues to snowball into bigger problems.
Higher Maintenance Costs
An increase in maintenance and repair costs is another clear indicator that your current strategy needs improvement. When businesses fail to conduct regular maintenance, they are often forced to pay for emergency repairs and expensive replacements. Over time, these costs can significantly outweigh the savings from skipping scheduled maintenance tasks.
Frequent Breakdowns of Key Assets
If key pieces of equipment are breaking down more frequently than expected, it’s likely due to missed maintenance tasks. Routine checks and servicing are designed to catch potential problems early, preventing them from escalating. If breakdowns are becoming the norm, it’s time to reassess your maintenance approach.
How to Prevent Missed Maintenance Tasks
Preventing missed maintenance tasks begins with a proactive mindset and the implementation of effective strategies. First and foremost, businesses should prioritize developing a well-structured maintenance schedule that aligns with the specific needs of their equipment, infrastructure, and overall operations. By conducting regular inspections and assessments, companies can identify potential issues before they become larger problems. Furthermore, using automated reminders and alerts can significantly reduce the risk of missed maintenance tasks, ensuring that every task is addressed on time. This proactive approach not only helps maintain operational efficiency but also prevents costly downtime due to equipment failure.
In addition to scheduling, utilizing the right tools is essential for staying on track. Maintenance management software is one of the most powerful solutions for streamlining the maintenance process. This software allows businesses to centralize their maintenance schedules, track completed tasks and monitor equipment performance in real-time. By integrating this technology, companies can easily generate reports, analyze trends, and make data-driven decisions about future maintenance needs. Ultimately, adopting these tools will help ensure that no task slips through the cracks, keeping operations running smoothly and efficiently.
Using Digital Tools for Better Scheduling
One of the best ways to prevent missed tasks is by using digital tools to automate maintenance scheduling. Platforms like Onfra offer a centralized system where you can schedule, track, and manage maintenance tasks efficiently. These tools can send automatic reminders, generate reports, and ensure that tasks are completed on time.
Digital scheduling tools can also prioritize maintenance tasks based on the criticality of the equipment, ensuring that essential machinery receives attention first.
Implementing Clear Communication Protocols
Clear communication is key to ensuring that maintenance tasks are completed as planned. Establish communication protocols between departments and external contractors to ensure that everyone is on the same page. A centralized system, such as Onfra, allows team members to access real-time updates and schedules, improving collaboration and reducing miscommunication.
Leveraging a Centralized Management System
A centralized management system like Onfra ensures that all maintenance tasks are tracked in one place. With this system, you can easily see which tasks are due, monitor progress, and receive notifications if something is missed. This reduces the risk of forgotten tasks and ensures that all departments are aware of the maintenance schedule.
The Role of Technology in Maintenance Management
Technology has transformed the way businesses approach maintenance. By leveraging digital tools, companies can automate processes, reduce human error, and ensure that tasks are completed on time.
The Importance of Automation in Task Scheduling
Automation is one of the most powerful tools in maintenance management. Automated scheduling systems like Onfra allow businesses to create recurring maintenance tasks, set reminders, and receive real-time notifications when a task is due. This takes the guesswork out of maintenance planning and ensures that nothing is overlooked.
Automated systems also provide a level of consistency that manual processes can’t match. By setting up automated schedules, businesses can rest assured that maintenance tasks will be completed at the right intervals, reducing the risk of equipment failure.
Real-time Monitoring with IoT Devices
The integration of IoT (Internet of Things) devices into maintenance management has revolutionized the way businesses monitor their assets. IoT devices can provide real-time data on the condition of equipment, allowing maintenance teams to detect potential issues before they become serious.
For example, sensors attached to machinery can monitor temperature, vibration, and other key metrics. If something falls outside of the normal range, the system can trigger an alert, prompting the maintenance team to take action. This kind of proactive maintenance can prevent costly breakdowns and reduce downtime.
The Benefits of Cloud-Based Systems for Maintenance
Cloud-based maintenance systems offer flexibility and scalability. With cloud-based platforms like Onfra, maintenance teams can access schedules, reports, and data from anywhere, ensuring that tasks are completed even when team members are working remotely.
Cloud systems also allow businesses to scale their maintenance operations as they grow. Whether you’re managing a single office or multiple locations, a cloud-based system can handle the complexity of your operations and provide real-time insights into the status of your assets.
Onfra – A Solution for Seamless Maintenance Management
Onfra is more than just a Visitor Management System (VMS); it’s a versatile platform designed to streamline various business processes, including maintenance management. By integrating maintenance scheduling with visitor management and desk booking, Onfra offers a comprehensive solution for businesses looking to improve their operational efficiency.
How Onfra Can Help with Task Scheduling
With its automated scheduling features, Onfra ensures that no maintenance task is missed. You can set up recurring tasks, assign responsibilities, and receive notifications when a task is due. This reduces the risk of oversight and ensures that your equipment and workspaces are always in top condition.
Integration with Desk Booking for Workspace Maintenance
Onfra’s integration with desk booking allows businesses to schedule maintenance tasks around workspace usage. For example, when an employee books a desk, the system can automatically trigger a maintenance task, such as cleaning or inspection, ensuring that workspaces are ready for use.
This level of automation simplifies the process of managing office spaces and ensures that maintenance tasks are completed without disrupting daily operations.
Conclusion: Take Control of Your Maintenance Strategy
Missed maintenance tasks can have serious consequences, from costly repairs to operational downtime. However, by adopting a proactive approach and leveraging technology, businesses can ensure that all maintenance tasks are completed on time.
Platforms like Onfra provide the tools you need to streamline your maintenance processes, improve communication, and reduce human error. Whether you’re managing a single location or multiple offices, Onfra offers a comprehensive solution that keeps your operations running smoothly.
FAQs
- What happens if a maintenance task is missed?
Missed maintenance tasks can lead to equipment breakdowns, increased downtime, and higher repair costs. Over time, neglecting maintenance can reduce equipment lifespan and compromise workplace safety. - How does technology improve maintenance management?
Platforms like Onfra improve maintenance management by automating task scheduling, providing real-time monitoring, and facilitating better communication between teams, ensuring tasks are completed efficiently. - Can Onfra be used across multiple locations?
Yes, Onfra is a cloud-based platform, allowing businesses to manage maintenance tasks across multiple locations with real-time access to schedules and updates. - What is the advantage of integrating desk booking with maintenance?
By integrating desk booking with maintenance, businesses can automate cleaning, inspections, and technical servicing based on desk usage, ensuring workspaces are always ready for use. - How do I ensure maintenance tasks are not overlooked?
To prevent missed tasks, implement digital tools like Onfra for automated scheduling, real-time notifications, and task tracking, along with fostering a culture of accountability.
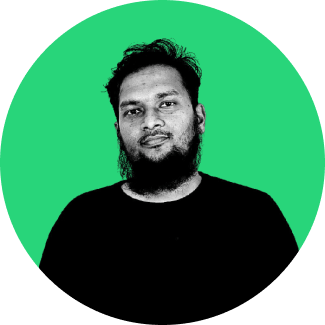
Rahman, CTO of onfra.io, drives technological advancements and strategic vision. With a focus on cutting-edge solutions, Rahman spearheads the development team at onfra.io, shaping the future of visitor management technology.